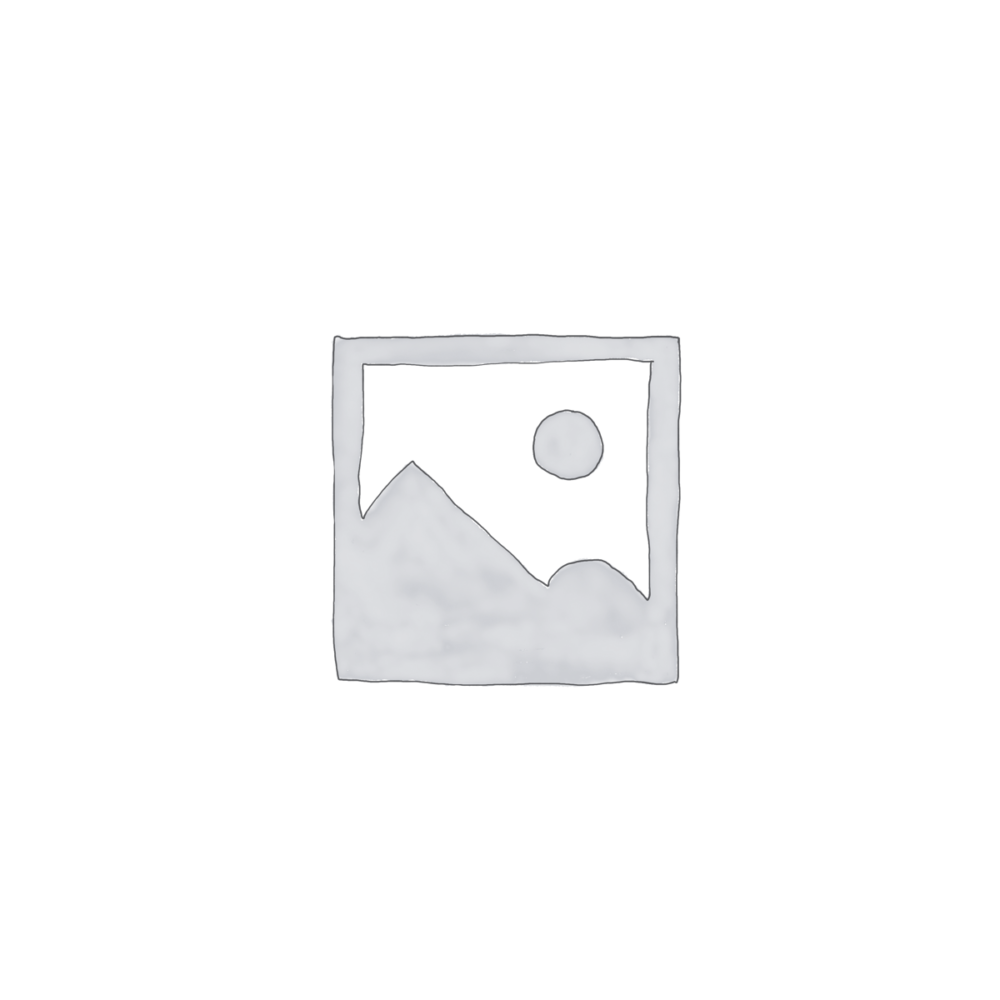
Galvanizing plants are a type of industrial facility where metal is treated with a protective coating of zinc to prevent it from corroding. The process of galvanizing requires the use of zinc, which is a pollutant source and can generate airborne contaminants such as particulates, sulphur oxides, and volatile organic compounds. These particulates and other contaminants are emitted during the galvanizing process and need to be controlled.
Description
Galvanizing plants are a type of industrial facility where metal is treated with a protective coating of zinc to prevent it from corroding. The process of galvanizing requires the use of zinc, which is a pollutant source and can generate airborne contaminants such as particulates, sulphur oxides, and volatile organic compounds. These particulates and other contaminants are emitted during the galvanizing process and need to be controlled. To reduce the number of emissions, galvanizing plants should employ effective control technologies such as scrubbers, baghouses, and fabric filters. Additionally, businesses should also use best practices such as preventing spillage, reducing emissions from quenching activities, and controlling emissions from the air exhaust of the furnace.
Fair Engineering Co. (FEC’s) designed Galvanizing plant FES system is useful to capture fumes emanating from around the source in any direction using newest designed hoods. In galvanizing plant, the hood is located on the side wall of the tank just above the zinc liquid. The material to be galvanized is dipped into the tank containing hot zinc when the material comes into the contact the fumes (zinc oxide) are generated which are absorbed by the specially designed hood. A ducting system is provided to transfer the particulate contaminant directly to bag house systems for efficient cleaning. The clean air with particulate matter of 50mg/Nm3 is released back to atmosphere through a stack.